As lockdown restrictions lift there is scope for this sector to bounce back, but questions remain around the future of infrastructure investment, owing to the likelihood of governments having to shell out on social spending programmes. What’s more, the knock-on effects of a damaged construction sector could reverberate throughout many others. To understand more about what these could be, Third Bridge Forum interviewed numerous experts working in these areas.
One aspect of construction that this cessation of activity could continue to disrupt is the cement industry. Overcapacity has been recognised as a global issue for years, and Europe is no exception. According to a former head at LafargeHolcim Ltd, 5-10 million tonnes of supply could be removed from Germany, 10 million tonnes from Italy and 15 million tonnes from Spain. Smaller countries, such as Greece, could also lose capacity.
Out of these, Germany is considered the most oversupplied. In order to stave off price collapse, reducing capacity is imperative. However, it’s difficult to get the industry to collectively decide on this and “it ends up being a game of who blinks first, which tends to be quite painful for everybody”. Smaller players, which make up about 40% of the market in Germany, are the most likely to be squeezed in this situation, as “in theory, the larger companies, the Heidelbergs and LafargeHolcims, should have advantages because of their technical capability and their procurement capabilities, which should allow them to keep their manufacturing costs lower than others.”
This pressure adds to sustainability concerns, and as a result cement’s future could be drying up. “If you put aside the coronavirus, the cement industry has some significant challenges in how it’s perceived in terms of a sustainable construction material.” If the cement industry’s carbon dioxide emissions were ranked alongside countries, it would be the world’s third-largest source. As a result, some companies, such as Heidelberg, are moving towards aggregates, which “don’t have the same kind of CO2 issue”.
Another sector that depends on construction activity is builders’ merchants. With consumers anticipating the lockdown, DIY and builders merchants in the UK saw a surge in sales earlier this year – now, however, “at best companies are trading sub-50% and many businesses have decided that they can’t manage with the restrictions” explained a former senior executive from Travis Perkins plc.
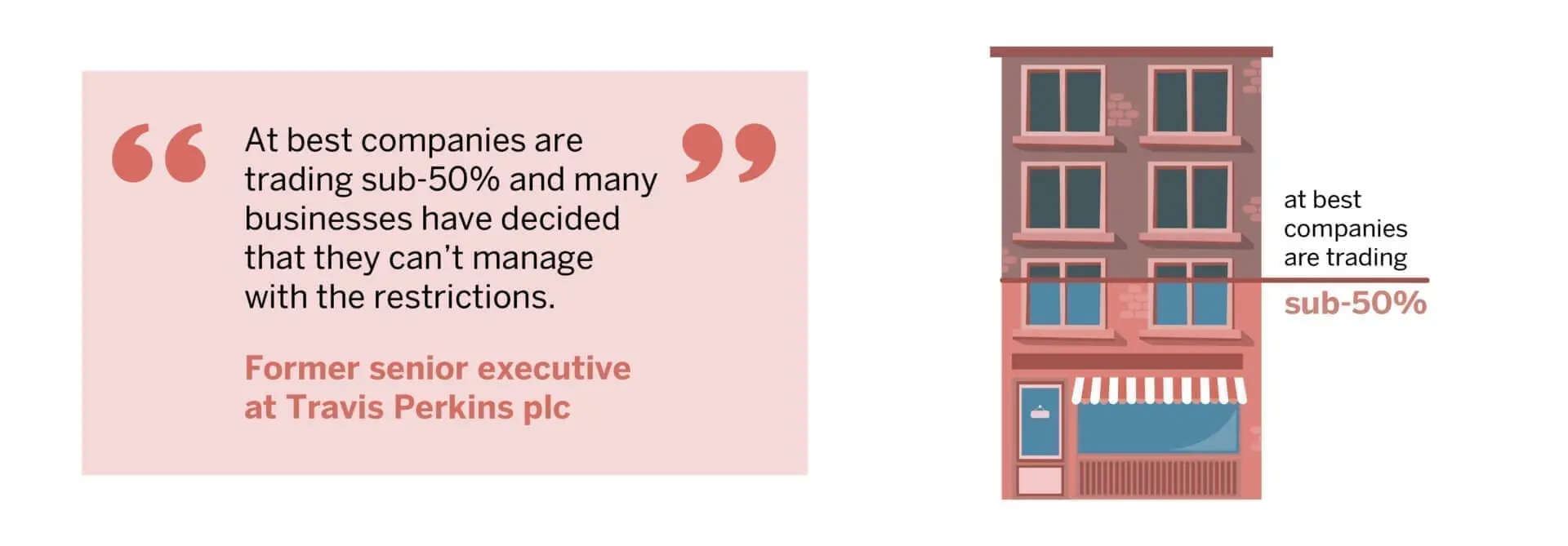
All fittings categories, from primary structural products to first fix, will come under pressure. However, the aforementioned senior executive believes that finishings will be “where it’s most competitive and most challenging”. With finishing fittings “predominantly imported – often from low-cost countries like China” – it makes sense there will be more competition here as builders look to cut costs. This is compounded by the fact that “first-fix manufacturers tend to be UK driven with UK raw materials. Because of their heavy weight and low value, relative to other products, they stay quite local.”
Travis Perkins, a builders’ merchant and home improvement retailer, experienced a YoY drop in revenue of about two-thirds in the first three weeks of April this year. According to a former director from Travis Perkins plc, there could be even lower operating levels across the rest of the industry. They added that, “all of those businesses are trying to open up, but actually this is a sector where there are some genuine difficulties in managing social distancing, both in terms of the operation of the branch and in terms of operation of the sites.”
For builders’ merchants like Travis Perkins, supplying housing construction companies is a “bit-part operation”. These companies now tend to go direct for supplies – the former director estimated that, at a peak, the main house builders would have constituted about a tenth of merchants’ sales. Consequently, when looking at indicators for building merchants’ recovery, the importance of housing transactions exceeds that of new builds. “RMI [renovation, maintenance and improvement] is driven by housing transactions… and that adds up to close to three times the value of the complete new-build sector.”
Any deterioration to consumer confidence resulting from the coronavirus pandemic could therefore affect building merchants. The aforementioned specialist compared this situation with the 2008-09 financial crisis to gauge if the same indicators could be relied on. “What we’d found over many years was that we needed to lag the growth of housing transactions by nine months to get an indication of the growth in the market. When the downturn hit, that lag extended to 12 months and then when the recovery started that lag collapsed to three months, but then over the following two years then extended back out to nine months.” The lag period, they explained, can be attributed to home buyer confidence and availability of disposable income.
Although significant uncertainties remain around COVID-19 and how long it will last, the strain is already being felt across many aspects of the construction industry. However, while waiting for the “new normal”, it appears that some opportunities – from new building materials to DIY uptake – are starting to reveal themselves.
The information used in compiling this document has been obtained by Third Bridge from experts participating in Forum Interviews. Third Bridge does not warrant the accuracy of the information and has not independently verified it. It should not be regarded as a trade recommendation or form the basis of any investment decision.
For any enquiries, please contact sales@thirdbridge.com